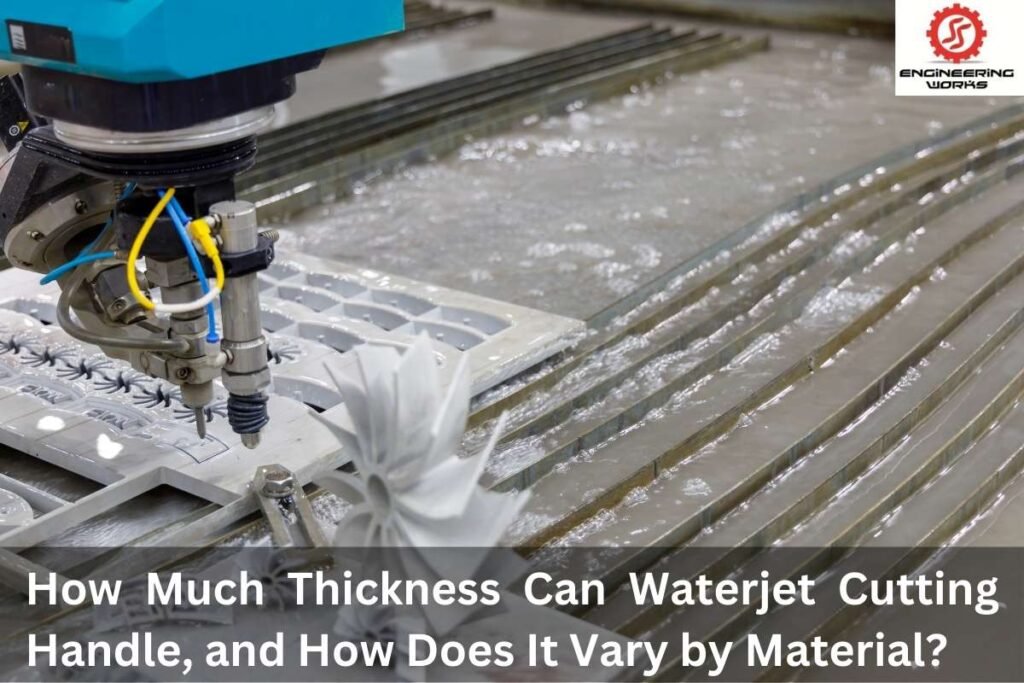
Regarding precision cutting, few technologies match the versatility and accuracy of waterjet cutting. Known for its ability to slice through a wide range of materials, waterjet cutting is widely used across industries for its efficiency and ability to handle various thicknesses.
But how thick can a waterjet cut? And how does this capability vary depending on the material?
Let’s explore these questions in depth.
What Factors Influence the Upper Thickness Limit for Waterjet Cutting?
The thickness of a water jet depends on several factors. While this cutting method is robust, its performance is influenced by material properties, cutting speed, and abrasive quality. Here’s a breakdown of these key factors:
1. Material Hardness
The hardness of the cut material significantly affects how thick a water jet can go. Softer rubber or foam can be cut much thicker than complex materials like steel or titanium. More rigid materials require more abrasive and water pressure to penetrate, which can limit the practical cutting depth.
2. Cutting Speed
The speed at which the water jet moves across the material is critical. Slower cutting speeds allow the water jet to penetrate deeper, making it possible to cut thicker materials. However, this also increases the cutting time, potentially affecting productivity for large-scale projects.
3. Abrasive Quality
In abrasive waterjet cutting, the quality of the abrasive material impacts the cutting performance. High-quality abrasives with consistent grain sizes can make clean, deep cuts more efficiently, while low-quality abrasives may reduce the maximum thickness achievable and compromise the cut’s precision.
4. Water Pressure
The pressure of the water jet—often exceeding 60,000 PSI in industrial applications—is another critical factor. Higher water pressure results in a more powerful jet, enabling the cutting of thicker materials with greater accuracy.
5. Time Required to Penetrate the Material
The time the waterjet spends on a single point also determines its cutting capability. When dealing with highly thick materials, the water jet may need to pause or slow down to allow the abrasive stream to penetrate fully. This factor is especially important when cutting dense or layered materials.
How Thick Can Waterjet Cut?
Waterjet cutters can achieve cuts ranging from 25 to 30 cm (10 to 12 inches) in hard materials.
Also Waterjet cutting is incredibly versatile, but the thickness it can handle varies depending on the material. Let’s break this down by specific materials:
How Thick Can a Water Jet Cut Steel?
In most cases, Waterjet cutting can handle steel thicknesses up to 12 inches (300 mm). The practical limit for structural steel and hardened alloys often lies between 6-8 inches, depending on the desired precision and project requirements. Cutting thicker steel may involve slower cutting speeds and higher-quality abrasives to maintain accuracy and edge quality.
How Thick Can a Water Jet Cut Aluminum?
Aluminum is softer and less dense than steel, allowing waterjet cutting to handle thicknesses up to 10-12 inches. Aluminum’s lightweight and malleable properties make it easier to cut at greater thicknesses than harder metals. Even with thicker cuts, waterjet cutting ensures smooth, burr-free edges on aluminum.
How Thick Can a Water Jet Cut Stone?
Waterjet cutting is widely used for natural and engineered stones, including granite, marble, and quartz. It can cut stone materials up to 8-10 inches thick. The high-pressure water combined with abrasives ensures precise cuts without causing fractures in the stone. This makes it preferred for intricate stonework, such as countertops and decorative pieces.
How Thick Can a Water Jet Cut Soft Materials?
Soft materials like rubber, foam, or plastics can be cut at significantly greater thicknesses. Waterjet cutting can sometimes handle materials as thick as 12-15 inches. These materials require lower water pressure and do not need abrasives, allowing quick and efficient cutting without damaging the material.
How Thick Can a Water Jet Cut Copper?
Copper is a dense yet relatively soft metal, making it suitable for waterjet cutting copper. Thicknesses up to 6-8 inches are achievable for copper. The process ensures precision without generating heat, crucial for materials like copper that can deform under high temperatures.
How Thick Can a Water Jet Cut Hard Plastics?
Hard plastics like acrylic or polycarbonate can be cut 4-6 inches thick with water jets. The key is to adjust the water pressure and cutting speed to prevent heat buildup, which could deform the material. Waterjet cutting is beneficial for plastics as it avoids the melting or warping common with laser cutting.
Abrasive Waterjet Cutting
Abrasive waterjet cutting—where abrasive particles are mixed with high-pressure water—is ideal for cutting thicker and more rigid materials. It excels in metals, ceramics, and composites, with thickness capabilities often exceeding 6-8 inches. This method provides clean cuts and is highly effective for intricate designs or tight tolerances in dense materials.
Pure Waterjet Cutting
Pure waterjet cutting uses only water without abrasives and is typically reserved for softer materials like foam, rubber, or thin plastics. It is unsuitable for cutting hard or thick materials, as its lack of abrasives limits its cutting power. However, pure waterjet cutting is unmatched for applications requiring precision in delicate or lightweight materials.
Which Industries Need Waterjet Cutting for High-Thickness Materials?
Industries that require precision and the ability to cut through high-thickness materials rely heavily on waterjet cutting. Here’s a closer look at how various industries benefit from this advanced technology:
Below image are the Industries that need waterjet cutting for high-thickness material:
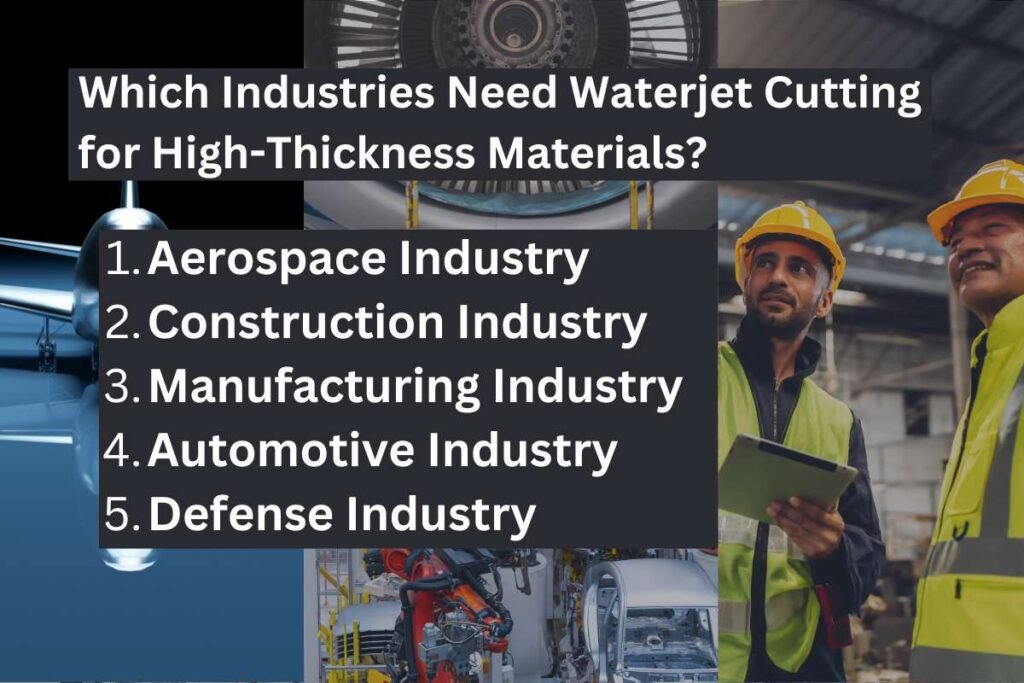
- Aerospace Industry: Waterjet cutting is vital for creating complex components from titanium, aluminum, and advanced composites. These materials are often thick; waterjet cutting ensures precision without inducing stress or heat damage.
- Construction Industry: Architectural applications, such as cutting thick stone, granite, or marble slabs, depend on waterjet cutting. It ensures clean and accurate cuts for decorative and structural pieces.
- Manufacturing Industry: This sector uses waterjet cutting to fabricate machine parts and components from thick steel, copper, and other metals. Its ability to handle diverse material thicknesses makes it an essential tool.
- Automotive Industry: Waterjet cutting is integral to producing high-quality automotive components, from cutting thick metal sheets to processing composite materials.
- Defense Industry: Cutting armored materials and producing precise parts for military vehicles or equipment requires the versatility and accuracy of waterjet cutting.
Limitations of Other Cutting Machines
While waterjet cutting excels in handling high-thickness materials, other methods face significant limitations. Here’s how they compare:
Laser Cutting
- Thickness Limit: Laser cutting is typically limited to materials up to 1 inch thick for steel and 0.5 inches for aluminum.
- Limitations: This method struggles with reflective materials like copper and requires substantial heat input, which can warp thicker materials. It is also less effective for materials like stone or composites.
Plasma Cutting
- Thickness Limit: Plasma cutting can generally cut metals up to 2 inches thick.
- Limitations: Plasma cutting lacks the precision of waterjet cutting and cannot handle non-metal materials such as stone or plastic. The edges are often rough and may require additional finishing.
EDM (Electrical Discharge Machining)
- Thickness Limit: EDM works best for more minor, precise cuts but is impractical for large thicknesses.
- Limitations: This method only works on conductive materials and is significantly slower than waterjet cutting. Its limited versatility makes it unsuitable for many applications requiring high-thickness cuts.
What Cannot Be Cut by a Waterjet?
While waterjet cutting is a versatile technology, it does have limitations. One of the most notable exceptions is tempered glass.
Tempered glass undergoes a heat treatment process that creates internal stresses, making it highly durable and resistant to impacts. However, these same internal stresses cause tempered glass to shatter when subjected to the high-pressure stream of a water jet.
The precise cutting force disrupts the balance of internal stresses, leading to fragmentation instead of a clean cut.
Choose us for top-quality waterjet cutting services! We offer precise, reliable cutting solutions for all, with fast and dependable delivery
Conclusion
Waterjet cutting is a powerful, flexible technology that handles various materials and thicknesses. By understanding the factors that influence its cutting capabilities—material hardness, cutting speed, abrasive quality, and water pressure—you can maximize its potential for your specific needs.
At SS Engineering Works, we specialize in delivering precision waterjet cutting services tailored to various industries. From aerospace to manufacturing, we provide cutting solutions that meet high quality, accuracy, and efficiency standards.
Whether it’s steel, aluminum, stone, or soft materials, our expertise ensures that your project requirements are met with perfection.
Trust SS Engineering Works for innovative waterjet cutting solutions.
FAQs About Waterjet Cutting
Waterjet cutting can handle thicknesses up to 12 inches for most materials, depending on material hardness, cutting speed, and water pressure. Softer materials like foam can be cut even thicker.
Waterjet cutting uses various materials, including metals, stone, glass, and plastics. However, it cannot cut tempered glass due to its internal stresses.
Waterjet cutting is exact, with tolerances as tight as ±0.003 inches, making it ideal for intricate designs and detailed applications.
Waterjet cutting is environmentally friendly as it produces no harmful fumes or heat-affected zones and minimizes material wastage.
At SS Engineering Works, we offer advanced waterjet cutting technology combined with experienced craftsmanship. Our commitment to quality, accuracy, and customer satisfaction ensures we deliver the best solutions for your needs