Water jet cutting is a revolutionary technology widely used in various industries for precise and efficient material cutting. Its ability to handle a wide range of materials with unparalleled accuracy has made it a preferred choice over traditional cutting methods.
This blog will explore the history of water jet cutting, how it works, and its many benefits. We’ll also compare it with other technologies, such as lasers and plasmas.
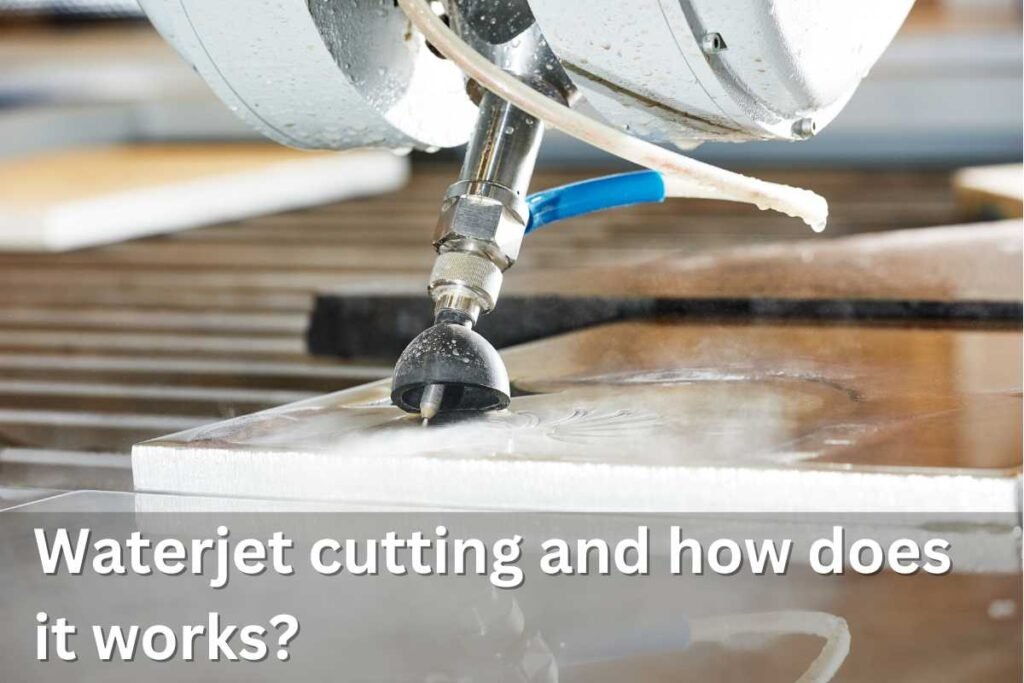
What is Water Jet Cutting?
Water jet cutting is a cutting-edge technology that uses a high-pressure stream of water to slice through various materials with precision and efficiency. Unlike traditional cutting methods, which generate heat and may alter the material’s properties, water jet cutting is a cold-cutting process that ensures the material remains intact.
This process forces water through a tiny nozzle at extremely high pressures, typically ranging from 30,000 to 90,000 psi (pounds per square inch).
A fine abrasive, such as a garnet, is added to the water stream for tougher materials like metals or stone. Thanks to its versatility and cost-effectiveness, water jet cutting is used extensively in aerospace, automotive, construction, and manufacturing industries.
This enhances the water jet’s cutting ability, making it capable of cutting through materials like steel, titanium, ceramics, and glass.
Knowing the entire history of water jet cutting
The history of Water Jet Cutting spans over a century, evolving from basic high-pressure water applications to the advanced, versatile tool used today. Here’s a detailed timeline based on research:
Early Developments (Mid-1800s to Mid-1900s)
Hydraulic Mining
The concept of high-pressure water jets began in the mid-19th century, with miners using water streams to erode rock and soil during the California Gold Rush. These early systems were a precursor to modern water jet technologies.
1930s
Initial experiments with high-pressure water in industrial cleaning and soft material cutting emerged. However, the low reliability of high-pressure pumps and seals at the time could have improved these systems.
Pioneering Efforts (1950s–1970s)
1956
Dr. Norman Franz, a forestry engineer, patented a system to cut wood using a high-pressure water jet. While it wasn’t widely adopted, it laid the groundwork for future advancements.
1960s
High-pressure pump technologies improved, with companies like McCartney Manufacturing producing pumps for polyethylene production. These pumps later found applications in water jet cutting.
1971
John Olsen of Flow Industries developed the first practical water jet system for manufacturing, enabling the cutting of soft materials like paper and rubber.
Abrasive Water Jet Cutting Revolution (1980s)
1980
Dr. Mohamed Hashish introduced the addition of abrasive particles (like garnet) to water jets, enabling the cutting of harder materials such as steel, stone, and glass. This innovation transformed water jet cutting into a versatile machining tool.
1984
Hashish demonstrated that abrasive water jets could efficiently cut metals and composites. By the late 1980s, industries such as aerospace adopted the technology for high-precision tasks
Modern Era (1990s–Present)
1990s
Integration with CNC (Computer Numerical Control) systems allowed precise, automated cutting of intricate shapes. This era saw water jet cutting become a staple in manufacturing sectors like aerospace, automotive, and architecture.
2000s
Innovations focused on increasing water pressure (up to 90,000 psi) and improving nozzle technology. Micro-abrasive water jets emerged for cutting delicate or thin materials.
Present
Water jet cutting systems are now highly automated, eco-friendly, and capable of cutting virtually any material. They are widely used across industries ranging from medical device manufacturing to construction.
What are the types of water jet cutting machines?
Water jet cutting machines are powerful tools designed for precise material cutting. They are primarily categorized into pure water jet cutting machines and abrasive water jet cutting machines based on the cutting process and materials they are suited for.
Pure Water Jet Cutting
This method uses only water to cut through soft materials like foam, paper, rubber, and certain plastics. The absence of abrasives makes it ideal for cutting lightweight materials without causing any contamination or damage.
Abrasive Water Jet Cutting
In this method, an abrasive material like garnet is mixed with water to cut through hard materials such as metals, stone, ceramics, and composites. The abrasive enhances the water jet’s cutting power, making it suitable for applications requiring high precision and clean cuts.
What Are the Benefits of Water Jet Cutting?
The growing popularity of water jet cutting is largely due to its numerous benefits, which make it a preferred choice across many industries. Let’s explore these advantages in detail
The below figure is just a Benefit of Waterjet Cutting
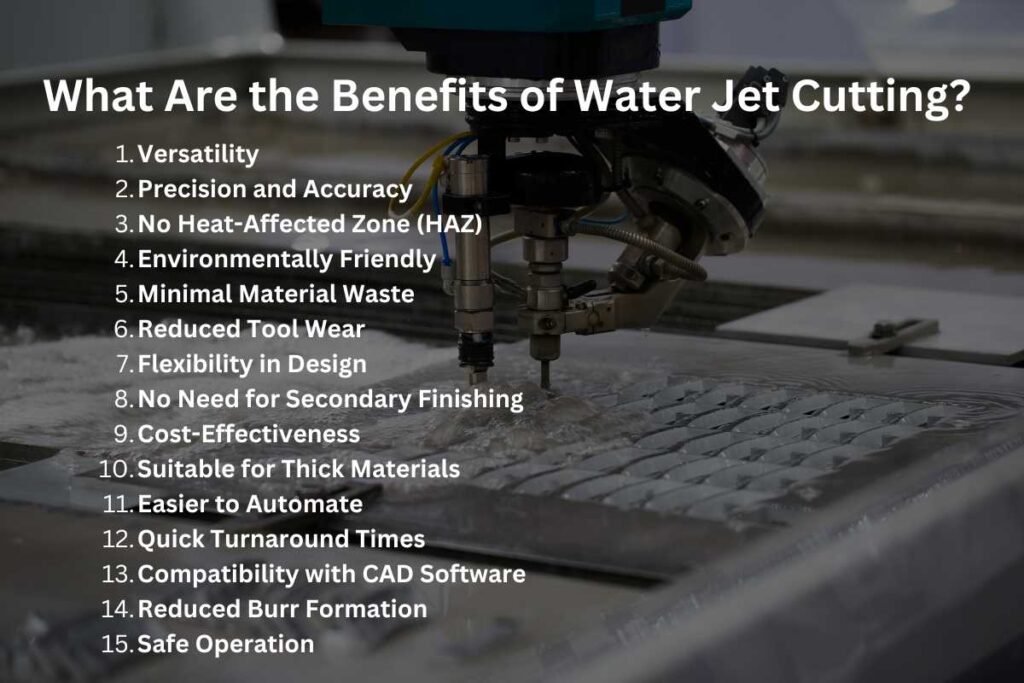
1. Versatility
Water jet cutting can handle a vast range of materials, including:
- Metals (aluminum, steel, titanium).
- Stone (granite, marble).
- Glass and ceramics.
- Composites and plastics.
- Soft materials like rubber, foam, and textiles.
This makes water jet cutting ideal for industries that require precision across multiple material types.
2. Precision and Accuracy
With cutting tolerances as tight as ±0.003 inches, water jet cutting ensures exceptional accuracy. Intricate designs and detailed cuts are easily achievable, making them suitable for high-end aerospace components and medical device manufacturing applications.
3. No Heat-Affected Zone (HAZ)
Since water jet cutting is a cold-cutting process, no heat is generated. This eliminates the risk of material warping, melting, or altering properties. It is especially advantageous for cutting heat-sensitive materials like composites or tempered glass.
4. Environmentally Friendly
Water jet cutting is considered one of the most eco-friendly cutting methods. Key reasons include:
- No harmful fumes or gases are produced.
- The water and abrasives used are non-toxic and can be recycled.
5. Minimal Material Waste
The process is highly efficient, with a narrow kerf (cut width). This minimizes material waste, saves costs, and reduces environmental impact.
6. Reduced Tool Wear
Unlike traditional methods, water jet cutting involves no direct contact between the cutting head and the material. This minimizes tool wear and reduces maintenance costs.
7. Flexibility in Design
Water jet cutting supports highly intricate and complex designs. Whether you need functional parts or decorative pieces, a water jet cutter can deliver exceptional results.
8. No Need for Secondary Finishing
Water jet cutting produces smooth, burr-free edges, eliminating the need for secondary operations like grinding or sanding.
9. Cost-Effectiveness
Despite its advanced capabilities, water jet cutting remains cost-effective. Factors like minimal material waste, low maintenance, and reduced labor contribute to its economic advantage.
10. Suitable for Thick Materials
Water jet cutting can penetrate materials up to 12 inches thick, making it ideal for heavy-duty applications like construction and shipbuilding.
11. Easier to Automate
Modern water jet cutting machines can be integrated with CNC systems, enabling automated, large-scale production with consistent quality.
12. Quick Turnaround Times
Water jet cutting’s speed and efficiency suit projects with tight deadlines. It ensures timely delivery without compromising precision.
13. Compatibility with CAD Software
Water jet cutting works seamlessly with CAD designs, allowing manufacturers to translate digital models into high-precision physical parts.
14. Reduced Burr Formation
Unlike traditional cutting methods, water jet cutting minimizes burr formation, producing clean, burr-free cuts.
15. Safe Operation
Water jet systems are safe to operate as they do not involve high temperatures, open flames, or harmful chemicals. With its unmatched advantages, water jet cutting has become a game-changer for industries requiring precise, efficient, and versatile material processing.
Choose us for top-quality waterjet cutting services! We offer precise, reliable cutting solutions for all, with fast and dependable delivery
Water Jet Cutting vs Laser Cutting
Water jet cutting and laser cutting are two advanced technologies, each with unique strengths. Water jet cutting uses a high-pressure stream of water, sometimes mixed with abrasives, to cut through various materials. In contrast, laser cutting relies on a focused laser beam to melt or vaporize materials. A key advantage of water jet cutting is that it doesn’t generate heat, avoiding material distortion or creating a heat-affected zone (HAZ). This makes it ideal for heat-sensitive materials like glass, composites, and metals.
Laser cutting, on the other hand, is excellent for thin materials such as acrylic, wood, and metals but struggles with thicker or reflective materials. Water jet cutting can cut materials up to 12 inches thick with smooth, burr-free edges that require no additional finishing.
Water jet cutting is also more eco-friendly as it doesn’t produce harmful fumes, unlike laser cutting. Water jet cutting is often better for projects requiring precision, versatility, and heat-free processing.
Water Jet Cutting vs Plasma Cutting
When comparing water jet cutting and plasma cutting, the main difference lies in the cutting process and material compatibility. Water jet cutting uses a cold cutting method, ensuring no heat-affected zones or material warping, while plasma cutting relies on heat to melt conductive materials like steel and aluminum.
Water jet cutting is more versatile and capable of cutting non-conductive materials like glass, ceramics, composites, and metals up to 12 inches thick. Plasma cutting is limited to conductive materials and is more suitable for quick, rough cuts on thinner metals (up to 2 inches). While plasma cutting is faster and more affordable for basic metalwork, water jet cutting provides superior precision, cleaner edges, and greater material flexibility.
Abrasive vs. Pure Water Jet Cutting
Water jet cutting is divided into two types: abrasive and pure water cutting. Abrasive water jet cutting combines high-pressure water with fine abrasives, such as garnets, to cut hard materials like metals, ceramics, and stone. It is slower than pure water cutting but highly precise, making it ideal for demanding aerospace, automotive, and construction applications.
Pure water jet cutting uses only high-pressure water and is best suited for soft materials like rubber, foam, and textiles. This method is faster and more cost-effective for lightweight materials and eliminates the risk of abrasive contamination. While abrasive cutting is ideal for tough materials, pure water jet cutting excels at clean, efficient cuts for softer materials.
Water Jet Cutting vs EDM Cutting
Water jet cutting and EDM (Electrical Discharge Machining) are highly precise but differ in their applications. Water jet cutting uses high-pressure water, with or without abrasives, to cut all materials, while EDM relies on electrical discharges to cut conductive materials like metals.
A major advantage of water jet cutting is its ability to cut conductive and non-conductive materials, including glass, ceramics, and composites. Unlike EDM, water jet cutting generates no heat, avoiding heat-affected zones and material distortion. Water jet cutting is also faster and capable of cutting materials up to 12 inches thick, whereas EDM is slower and limited to thinner materials.
While EDM is ideal for ultra-fine, intricate cuts, water jet cutting’s versatility, speed, and heat-free process make it the preferred choice for a broader range of industrial applications.
Conclusion
Water jet cutting has transformed modern manufacturing by offering a precise, versatile, and eco-friendly solution. Whether cutting intricate designs in soft materials or slicing through thick metals, water jet cutting remains unmatched in its capabilities.
Manufacturers can make informed decisions to improve efficiency and product quality by understanding its history, technology, and benefits.
For more information about water jet cutting services, feel free to reach out to SS Engineering Works—your trusted partner in precision manufacturing!