Glass is one of the most versatile materials used in various industries, ranging from architecture to electronics and art. It is formed by cooling molten silica rapidly, resulting in a transparent, brittle material. Despite its beauty and versatility, cutting glass is a challenging task.
Its brittle nature means it can easily crack, chip, or shatter under stress, making traditional cutting methods less effective and prone to damage.
This is where water jet cutting machines shine. They provide a modern, precise, and efficient solution for cutting glass without compromising its structural integrity.
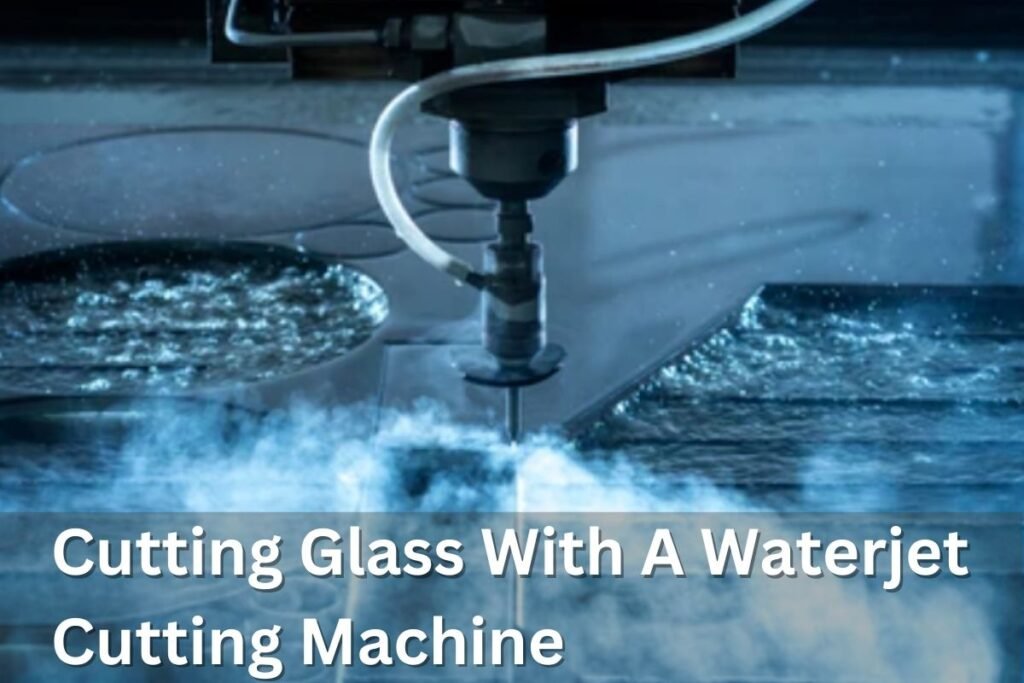
In this blog, we’ll explore how water jet cutting machines handle glass, their benefits, and how to choose the right service for your needs.
Can You Cut Glass With a Water Jet Cutter?
Yes, you can cut glass with a water jet cutter. In fact, water jet cutting is one of the most efficient and reliable methods for cutting glass, whether it’s for industrial purposes or intricate artistic designs.
Traditional methods like scoring and breaking glass often result in micro-cracks, uneven edges, or complete failure of the material. In contrast, water jet cutting uses high-pressure water mixed with abrasive materials to create a clean and smooth cut. This process minimizes the risk of cracking or damaging the glass.
With the ability to cut through various types of glass regardless of thickness, water jet cutters have become an indispensable tool for industries such as construction, automotive, and manufacturing.
How Waterjet Cutting Works for Glass?
Water jet cutting for glass involves using a stream of highly pressurized water combined with abrasives like garnet. This mixture allows the water jet cutter to carve through the glass with incredible precision and minimal stress. Let’s break down how the process works:
- High-Pressure Water Stream: The cutting machine generates a high-pressure water stream—ranging from 50,000 to 90,000 PSI. This water is directed through a narrow nozzle at supersonic speeds.
- Abrasive Materials in Action: Abrasive materials, like garnet, are added to the water stream to enhance its cutting ability. The abrasives act like tiny cutting tools, grinding through the glass with precision.
- Adjustable Pressure for Thickness: The pressure used during water jet cutting can be adjusted based on the thickness and type of glass being cut. Thicker glass requires higher pressure and more abrasive material, while thinner or delicate glass may need lower pressure to prevent cracking.
What Are the Types of Glass Suitable for Waterjet Cutting?
Water jet cutting is highly versatile and can handle a wide range of glass types. However, not all glass is suitable for this method. Let’s explore which ones work best:
Types of Glass That Can Be Cut with Waterjet
- Annealed Glass: This is the most basic type of glass, often used in windows, doors, and tabletops. Since annealed glass doesn’t have internal stress, it’s one of the easiest to cut with water jets.
- Laminated Glass: Comprising two or more layers of glass bonded with an interlayer, laminated glass can be cut effectively. The water jet’s precision ensures clean cuts through the layers while maintaining the laminate’s integrity.
- Stained or Decorative Glass: Commonly used in art and interior design, stained glass can be intricately shaped with water jets to create unique patterns and designs.
- Frosted Glass and Mirrors: Water jet cutting preserves the finish on frosted glass and mirrors, making it ideal for applications requiring smooth, aesthetic results.
- Bulletproof and Specialty Glass (With Limitations): Thick, high-strength glass, like bulletproof glass, can be cut, but it requires advanced machinery, higher pressure, and more abrasive material, making it time-consuming.
Types of Glass That Can’t Be Cut with Waterjet
- Fully Tempered Glass Without Perforations: Tempered glass is under immense internal stress. Cutting it directly can lead to shattering, as the stress is unevenly released.
- Overly Thick Glass: While water jets can cut thick materials, extremely thick glass may require multiple passes, leading to time and material inefficiencies.
What Are the Benefits of Using a Waterjet to Cut Glass?
Using water jet cutting for glass provides numerous advantages over traditional cutting methods. Here are some of the key benefits:
The below figure is just a Benefit of Waterjet Cutting with glass
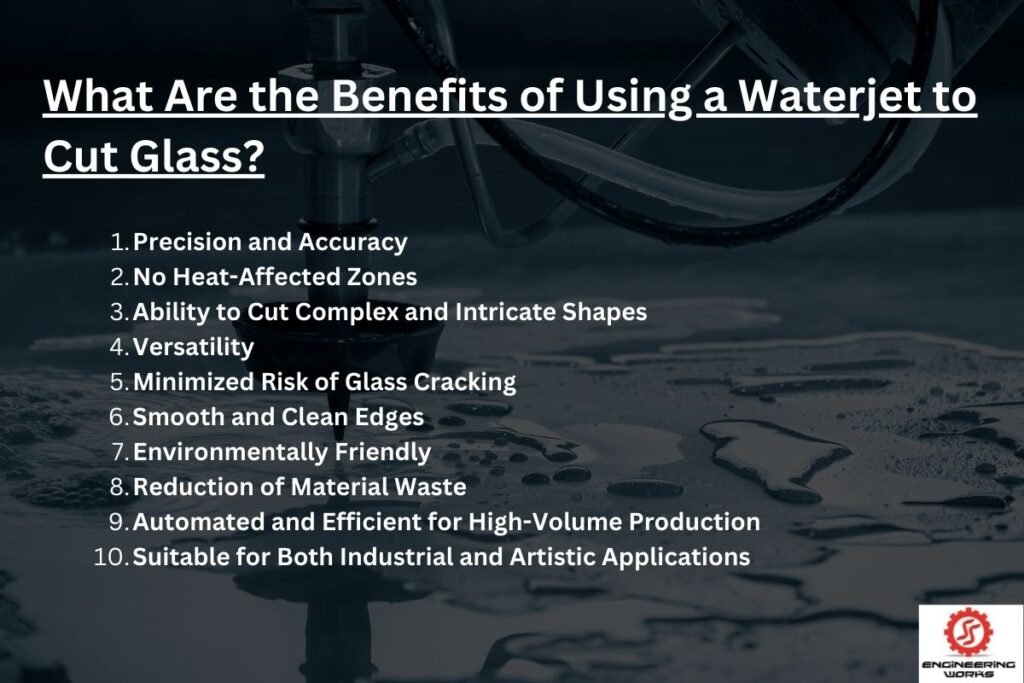
1. Precision and Accuracy
Water jet cutting ensures precise cuts, even for intricate or detailed designs. With tolerances as low as ±0.005 inches, it’s perfect for projects requiring high accuracy.
2. No Heat-Affected Zones
Unlike laser cutting or other heat-based methods, water jet cutting doesn’t produce heat. This eliminates the risk of warping, discolouration, or internal stress in the glass.
3. Ability to Cut Complex and Intricate Shapes
Water jets are incredibly versatile and capable of creating curved, intricate, and custom shapes. This is ideal for artistic and decorative applications.
4. Versatility
From delicate stained glass to thick laminated glass, water jet cutters can handle a wide variety of materials.
5. Minimized Risk of Glass Cracking
The low-stress nature of the process ensures that the glass doesn’t crack or shatter, reducing waste and increasing success rates.
6. Smooth and Clean Edges
The precision of water jet cutting leaves smooth, clean edges that don’t require additional finishing, saving time and effort.
7. Environmentally Friendly
Water jet cutting uses water and natural abrasives, producing no hazardous fumes or waste, making it a sustainable option.
8. Reduction of Material Waste
By offering precise cuts, water jet cutting reduces material waste, which is especially beneficial for costly or rare types of glass.
9. Automated and Efficient for High-Volume Production
With programmable settings, water jet machines can handle large-scale production efficiently while maintaining consistent quality.
10. Suitable for Both Industrial and Artistic Applications
Whether for architectural projects, industrial manufacturing, or custom art, water jet cutting is versatile enough to serve diverse purposes.
Choose us for top-quality waterjet cutting services! We offer precise, reliable cutting solutions for all, with fast and dependable delivery
Which Industries Are Using Waterjet Cutting for Glass?
Water jet cutting has become an indispensable tool in various industries that rely on precision, efficiency, and versatility in glass cutting. Its ability to handle intricate designs and different glass types without compromising quality makes it a popular choice across the following sectors:
1. Construction and Architecture
In the construction industry, water jet cutting is used to create glass panels for windows, doors, skylights, and facades. Architects rely on this method for designing decorative glass components, custom shapes, and intricate patterns that enhance the aesthetic appeal of buildings.
2. Automotive Industry
The automotive industry uses water jet cutting to cut laminated glass for windshields and car windows precisely. This process ensures the glass is shaped to exact specifications while maintaining safety and structural integrity, which is critical in vehicles.
3. Electronics and Technology
Glass components play a crucial role in electronic devices like smartphones, tablets, and flat-screen monitors. Water jet cutting enables manufacturers to produce these components with extreme accuracy, meeting the fine tolerances required in the electronics industry.
4. Interior Design and Furniture
Interior designers and furniture makers use water jet cutting to create decorative glass pieces such as tabletops, mirrors, partitions, and shelves. The clean and smooth edges produced by this process make it ideal for achieving professional and visually appealing finishes.
5. Art and Craft
Artists and artisans use water jet cutting for stained glass and custom designs. The precision allows them to cut intricate shapes, curves, and patterns that would be difficult or impossible to achieve with traditional methods.
6. Manufacturing and Industrial Applications
In manufacturing, water jet cutting is utilized to produce glass components for machinery, equipment, and other industrial applications. The process ensures precise cuts without compromising the strength of the glass.
What are the challenges of waterjet cutting for glass?
While water jet cutting is a highly efficient and precise method for cutting glass, it does present a few challenges that operators and service providers must address:
1. Glass’s Brittle Nature
Glass is inherently brittle, and improper handling during the water jet cutting process can lead to cracks, chips, or even shattering. Achieving the right balance of pressure and abrasive material is crucial to avoid damaging the glass.
2. Cutting Tempered Glass
Tempered glass is particularly challenging to cut because of its internal stress. Attempting to cut it directly with a water jet cutting machine can cause the entire sheet to shatter. In such cases, the cutting process must account for pre-existing perforations or alternative methods.
3. Tool Wear and Maintenance
The abrasive materials used in water jet cutting, such as garnets, can cause significant wear and tear on the nozzles and other components of the machine. This increases maintenance requirements and operational costs over time.
4. Thickness Limitations
While water jet cutting can handle a variety of glass thicknesses, extremely thick glass may require multiple passes. This can extend cutting times and increase the consumption of abrasives and energy, making the process less efficient for very thick materials.
5. Operator Skill and Expertise
Cutting glass with a water jet cutting machine requires skilled operators who understand the nuances of pressure adjustment, nozzle alignment, and abrasive selection. A lack of expertise can lead to suboptimal results, including poor-quality cuts or material waste.
How to Choose the Best Waterjet Cutting Service for Glass?
Selecting the right water jet cutting service provider is essential for achieving precise, clean, and high-quality cuts for your glass projects. Here are the key factors to consider when making your choice
1. Experience and Expertise
Choose a provider with extensive experience in water jet cutting for glass. Cutting glass is different from cutting other materials, and it requires specialized knowledge to adjust pressure, abrasive levels, and cutting speed based on the type and thickness of the glass.
2. Modern and Advanced Equipment
Ensure the service provider uses state-of-the-art water jet cutting machines. Modern equipment can handle a variety of glass types and thicknesses with greater precision, reducing the risk of cracking or chipping.
3. Customization Capabilities
Look for a provider who can meet your specific needs. Whether you require intricate artistic designs, industrial-scale production, or precise cuts for electronics, the service should offer the flexibility to accommodate your project.
4. Quality Assurance
A good service provider will guarantee high-quality results. Check reviews, certifications, and samples of their work to ensure they consistently deliver smooth edges, clean cuts, and defect-free results.
5. Turnaround Time
For projects with tight deadlines, select a provider who can deliver your work within the required timeframe without compromising on quality. Water jet cutting services that prioritize efficiency and professionalism are ideal for time-sensitive projects.
6. Competitive Pricing
Compare quotes from multiple water jet cutting providers to find one that offers a balance between cost and quality. While affordability is important, don’t compromise on quality to save costs, as poor-quality cuts can result in material waste or additional expenses.
7. Customer Support and Communication
Choose a provider with excellent customer support who can guide you through the process, offer recommendations, and address any concerns you may have. Clear communication ensures your requirements are understood and met effectively.
Conclusion
When it comes to cutting glass with precision, safety, and efficiency, water jet cutting is the gold standard. Whether you need to cut laminated glass, create intricate designs for decorative glass, or work on large-scale industrial projects, water jet technology offers unmatched versatility and accuracy.
At SS Engineering Works, we specialize in delivering top-quality water jet cutting services tailored to meet your needs. With years of expertise and advanced equipment, we ensure flawless results for all types of glass-cutting projects, whether industrial, architectural, or artistic.
If you’re looking for reliable and professional glass-cutting solutions, get in touch with SS Engineering Works today. Let us help you bring your vision to life with precision and excellence!
FAQs
You can use tools like a utility knife or diamond-tipped tool to score the mirror and snap it along the line. However, this can result in uneven edges or damage. For precise and smooth cuts, consider professional water jet cutting services.
Cutting tempered glass is challenging due to its internal stress, which can cause it to shatter. The best solution is to cut it before tempering. If working with tempered glass, consult professionals who use specialized methods like water jet cutting.
Laminated glass, with its multiple layers and interlayers, requires precision cutting. Water jet cutting is the ideal solution as it cuts through the layers cleanly without damaging the interlayer or causing misalignment.
Yes, water jet cutting is entirely safe for decorative glass. It prevents heat damage and ensures clean cuts, making it perfect for intricate designs, stained glass, and other artistic applications.
Not all glass types can be cut. Water jet cutting works well for annealed, laminated, stained, frosted glass and mirrors. However, tempered glass and highly thick glass require special considerations or alternative methods.